メンテナンスによる環境負荷の低減
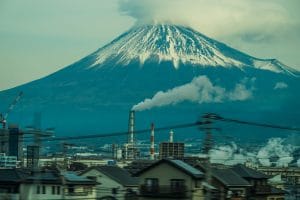
環境問題は現代の大きな問題の一つです。環境問題への取り組みを行っている企業も多くあるかと思いますが、機械のメンテナンスを行うことも環境への負荷を低減し、環境を維持することに貢献します。今回は機械のメンテナンスがなぜ環境負荷低減につながるのか、そしてそれを実現するにはどのようなことが必要なのかをご紹介いたします。
適切なメンテナンスが環境負荷を低減する
適切なメンテナンスが行われていることにより、以下のような理由から環境に与える負荷の低減が期待出来ます。
- 環境破壊のリスクを最小限にする
- 適切なメンテナンスが行われていない場合には摩擦などによる余計なエネルギー消費が発生し、発電による環境への負荷を高めることに繋がります。そのため、無駄のない稼働のためには適切なメンテナンスが重要です。
また、メンテナンスが不適切な場合、機器の破損により作動油などが環境に流出する、もしくは摩擦低減のために多くの潤滑油が必要となるなど、非効率というだけでなく、環境への悪影響も懸念されます。
- 適切なメンテナンスが行われていない場合には摩擦などによる余計なエネルギー消費が発生し、発電による環境への負荷を高めることに繋がります。そのため、無駄のない稼働のためには適切なメンテナンスが重要です。
- 生産コストの削減
- 適切なメンテナンスにより機械の予期せぬ停止を防ぎ効率的に稼働させることが出来ます。それによりダウンタイムの削減や消費電力の低減が期待できるだけでなく、廃棄物の発生要因を少なくすることにも繋がります。
- メンテナンス工数の低減
- 優れた設計・設置を行うことは時間がかかる場合があります。また、メンテナンス作業時につい手を抜いて作業時間を減らしたくなるかもしれません。しかし、適切な設計・設置・メンテナンスにより機械が効率的に稼働し、予期せぬ突発的なメンテナンス作業の発生が抑えられることでメンテナンスの総工数は低減されることでしょう。それにより日常点検などに集中することが出来るようになります。工数を削減してメンテナンススタッフを減らすということではなく、各スタッフのスキルを適切に活用するために重要です。
- メンテナンススタッフの安全上のリスクを低減
- 深刻な故障が発生した場合や大規模な重整備を行う場合、メンテナンススタッフに対する負荷や危険性は高くなってしまうことがあります。当然、安全対策を行った上で作業をすることになりますが、適切なメンテナンスにより機械の寿命を改善・向上することで重整備の間隔を長くすることが期待できます。重整備を行うよりも点検や予防保全作業のほうがスタッフに生じる危険性は小さくなると考えられます。
- 稼働エネルギーの低減
- 効率を考えて設計された機械であったとしても、ミスアライメントや過度の振動、潤滑不良などがあると稼働させるために余分なエネルギーが必要となります。適切なメンテナンスによってこれらのエネルギーの無駄を削減することが期待できます。
- 長寿命化
- 適切なメンテナンスにより機械に使用されている個々の部品の長寿命化が期待できます。ベアリングやシールなどを交換するとそれらの廃棄・埋め立てが必要となりますが、長寿命化により交換頻度が低下すれば廃棄物発生を少なく抑えることができます。また、スペアパーツの保管も少なく出来るというメリットもあります。
適切なメンテナンスを行うための仕組みづくり
上述の通り、適切なメンテナンスを行うことで様々なメリットがあります。しかし、単に適切なメンテナンスを行えと言うだけでは実現出来ません。現状を把握し現場の改善を一歩ずつ進めていく必要があります。そのためのアクションとして以下のようなものを例示いたします。
- 現在のコストを明らかにする
- 電力の消費量やダウンタイム、修理が頻繁に行われている場面・機械の把握や、スペアパーツの使用量などを把握します。コストや時間の削減を試みる時にはまず現状を明らかにした上で対策を検討します。
- 問題が頻発する機械を特定する
- 工場全体ではなく特定の機械に対する改善から始めます。そのためにもまずは問題のある機械を特定します。その周囲の改善を行い実際に効果が出ることを確認し、効率・生産性を高めます。その後、他の機械の改善へと移ります。
- メンテナンストレーニングの必要性
- 単に一定時間のトレーニングを行うのではなく、実際に必要となるトレーニングを行うことが大切です。きちんとした精密メンテナンスの手順を知っているのか、それとも業務上誰かから学んだ不適切なメンテナンス手順を行っていないかなどを見極めて内容を設定します。
- 故障分析を行い、真の根本原因を把握する
- 機械に問題があることをわかっているだけでは不十分です。「なぜ」その不具合が発生したのかを調査しなくてはなりません。時間がなく単に故障部品を交換するだけで済ませたくなるかもしれませんが、機械を調査し根本原因を把握して原因を取り除くことは時間をかけてでも行うべき場合が多いです。
- 精密メンテナンスや信頼性向上に寄与する機器を導入する
- 適切なメンテナンスのためには機械の内部で何が起こっているのかをしっかりと理解して対応する必要があります。問題が起こり始めてすぐに検知し対処することで大規模な故障の発生を抑制したり、原因を究明することで再発頻度を減らすことに繋がります。振動診断装置や、レーザーアライメント装置、作動油解析装置や赤外線のサーモグラフィー、超音波可視化装置によるリークや異常放電の検知、電流解析などを活用することで機械の状態・効率・寿命を向上させることに寄与します。
- 潤滑油とオイルフィルターの適切な選択
- 潤滑油の有効寿命を延ばすことは、廃棄される潤滑油を減らし、無駄を省くことにも繋がります。
作業のための時間や費用は発生してしまいますが、適切なメンテナンスを行い機械の状態・効率・寿命の向上を実現することで、最終的には利益の増大や製品品質の向上、従業員への負荷低減などが期待できます。
これを実現するために、我々は振動診断装置やレーザーアライメント装置を通じて貢献していきます。