予知保全計画の重要な10ステップ
機械診断・監視 |
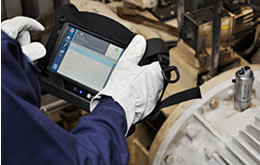
工場でのメンテナンス作業で求められることは機械・設備をきちんと使用可能な状態に維持管理することです。
工場にある多くの機械・設備を維持管理していくには多大な労力を必要とします。しかし、費用対効果の観点から言えば少ない労力で効率的に様々な機械・設備のメンテナンスを行うことが出来る体制づくりが求められます。
メンテナンスを効率的に行うための、様々な診断ツールや作業ツールがありますが、それらだけで全てが解決するわけではありません。熟練スタッフであれば効率的な作業が自ずと身についているかもしれませんが、そのような人材が限られている場合も多く、新たに加わったメンバーを含めたメンテナンスチームにどのように浸透させていくのかということも考えていく必要があります。
また、予知保全・状態監視を有効活用することでリソースを効率的に活用した保全活動を行うことが出来ます。以下に示した事後保全と予知保全・状態監視のメリットとデメリットをご覧いただくと、適切な予知保全・状態監視は効率的な保全に有効であるとご理解いただけると思います。
事後保全:
- メリット
- 見かけ上の(開始までの初期の)コストが低い
- トレーニングのコストが低い(個別事例への対処を覚えるだけのため)
- デメリット
- 意図せぬタイミングでの故障による稼働停止で損失が生じる
- 残業が必要になった場合、人件費が増加する
- 故障が他の機械やプロセスへの影響を及ぼす可能性。被害の増加
- スタッフの運用が非効率になる。故障時は多くの作業が必要となるが、通常時は修理作業が発生しない。
予知保全・状態監視:
- メリット
- 機械の状態に応じて最適なタイミングでメンテナンスを行うことができる。早すぎる交換を避け、致命的な状態にはさせない。
- 管理者によってメンテナンス計画を管理することができる。
- プラント全体の適切なスケジュール管理に繋がる
- 工場全体でのコスト削減(意図せぬ停止などを避けられる)
- メンテナンススタッフの作業も計画的に割り振ることが出来る。
- デメリット
- 初期費用が必要となるため、開始直後だけを見るとコストがかかっているように思える
- 状態監視装置の使用や結果評価のため、少なくともチームスタッフに適切なトレーニングが必要となる。
カール・ネルソンは著書『Millwrights and Mechanics Guide』の中で状態監視(予知保全)について「故障が発生する前段階において、測定したパラメータと既知の限界値とをスタッフが比較できるようにする装置」と説明しています。このような装置により、機械の状態を適切に把握し必要なメンテナンス作業を計画的に行うことが予知保全・状態監視であり、効率的な保全活動につながります。また、彼は状態監視を適切に行っていく方法として以下のような10ステップを提唱しています。
- 工場マップを作成し、全ての装置・機器の場所をリスト化します。
- 各機器に名称を付け、メンテナンスを行う際にどのようなルートを通るのか計画します。簡単に辿ることが出来るルートにすることが大切です。
- 実際に各機器を確認し、メーカー名や品番、シリアル番号などを適切に記録します。各機器の写真を撮ることも重要であり、カメラ機能付きの振動診断ツールやスマホ・タブレットを用いて振動診断を行うツールをお持ちの場合はそれを使うことも可能です。
- 各機器に使われている部品の仕様を確認するためにも、各機器のマニュアルをきちんと揃えます。手元にない場合はメーカーの協力が必要なこともあり得ます。
- ここまでで収集した情報をパソコン等に整理して集約します。この時点では必要性を感じないかもしれませんが、将来必要となった場合に素早く情報を見つけることが出来ます。
- 各機器のメンテナンス・修理に関わる主要なメンバーとの打ち合わせを行い、機器の情報や状態監視プランについての情報を共有します。チームできちんとプロセスを継続するためにも、全員にとって意味のある計画にしておくことが肝心です。
- 状態監視プランを策定し、各メンバーにタスクを割り振る準備が出来た状態です。漏れがある可能性もあるため、いきなり工場全体でプランを策定するのではなく、工場の一部でルート作成やプラン策定を行うことも一つの方法です。
- 工場全体に対して状態監視プランを策定します。
- 状態監視プランのあらゆる部分、ルートやタスクの割り当て、頻度、作業手順など様々な部分についてのフィードバックが行われるような体制を作ってください。プランを策定するだけでなく、それを継続し改善することも必要です。
- 状態監視プロセスを監査する体制も構築する必要があります。
適切なプランを構築ししっかりとそれを実行していくためには適切なツールの導入も重要です。振動診断ツールを使うことで経験を補ったり、機械による定量的な評価を行うことも可能となります。プラン策定の際には是非とも各種ツールについてもご検討ください。