正しくシムを追加しているのに……
アライメント |
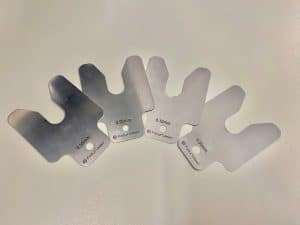
心出し作業では装置の脚部にシムを追加する作業が発生します。レーザーアライメントツールやダイヤルゲージなどによる測定で必要なシムの厚みを算出し、その厚みとなるように複数枚のシムを組み合わせて脚部に追加します。
正しい厚みとなるようにシムを追加したにもかかわらず、装置のアライメントが適切にならなかったことはありませんか?
残念ながら適切なシムの枚数を入れているはずですが、ミスアライメント状態になることは起こり得ます。計算ミスなのでしょうか。それとも測定がまずかったのでしょうか。
もしかすると追加したシムに問題があるのかもしれません。
同じ厚みであるはずのシムであったとしても、ごくわずかに厚みが異なります。人間の感覚では分からない厚みの違いであったとしても、アライメントを行うと差が生じることがあるのです。例えばその原因は製造プロセスで生じていることがあります。シムは大きなステンレス鋼のコイルから作られますが、コイルの部位により板厚がごく僅かだけ異なっているために、最終的なシムの厚みにも差が生じます。
もちろん、許容されたバラつきの範囲内ではあるはずですし、更にそのバラつきを小さく管理するとなると経済的に現実的ではありません。
心出しで用いるシムは薄いものを何枚も使用するのではなく、厚いものも使用し少ない枚数で対応するのが良いと言われていますが、各シムの厚みの微妙なバラつきのことを考えても、少ない枚数であることが望ましいと言えます。
また、古いシムを使用するということも問題の原因の一つです。古いシムに生じたバリや錆び、腐食などによりシムの厚みに影響が出ていることもあります。
人為的なミスで不適切なシムを使用しているということも考えられます。薄いシムが1枚余分に追加されていたとしても、その場では見逃してしまうかもしれません。もちろん、心出し時の確認で気づくかと思いますが、別の場所に入れるべきシムを誤って追加してしまわないような作業手順を心掛ける必要があります。例えばシムはそれぞれの脚に必要な厚みでセットし、事前に各脚の近くに置いておくなどの対応が望ましいでしょう。
ここまで述べてきた原因に対する対策の一つをご紹介します。それはシムの厚みを測定することです。マイクロメーターなどで実際に厚みを測定すると誤ったシムの挿入や個々のシムの製造のばらつきによる影響度合いを事前に知ることが出来ます。1枚1枚測るというわけではなく、積み重ねたシムの厚みを測定すれば余分なシムが含まれていた場合にもすぐに気づけるはずです。
アライメント作業の効率化のためには、作業時の重要なポイントをしっかりと把握し、適切なツールを利用することが大切です。ポイントはこれまでのブログ記事でもいくつかご紹介しているのでよろしければご覧ください。